3D printing has revolutionized the way we create and manufacture objects.
As the technology continues to evolve, new methods of communication between the printer’s hardware and software are being introduced.
One such method is UART (Universal Asynchronous Receiver/Transmitter) mode, which allows for dynamic control of stepper motors within a 3D printer.
Table of Contents
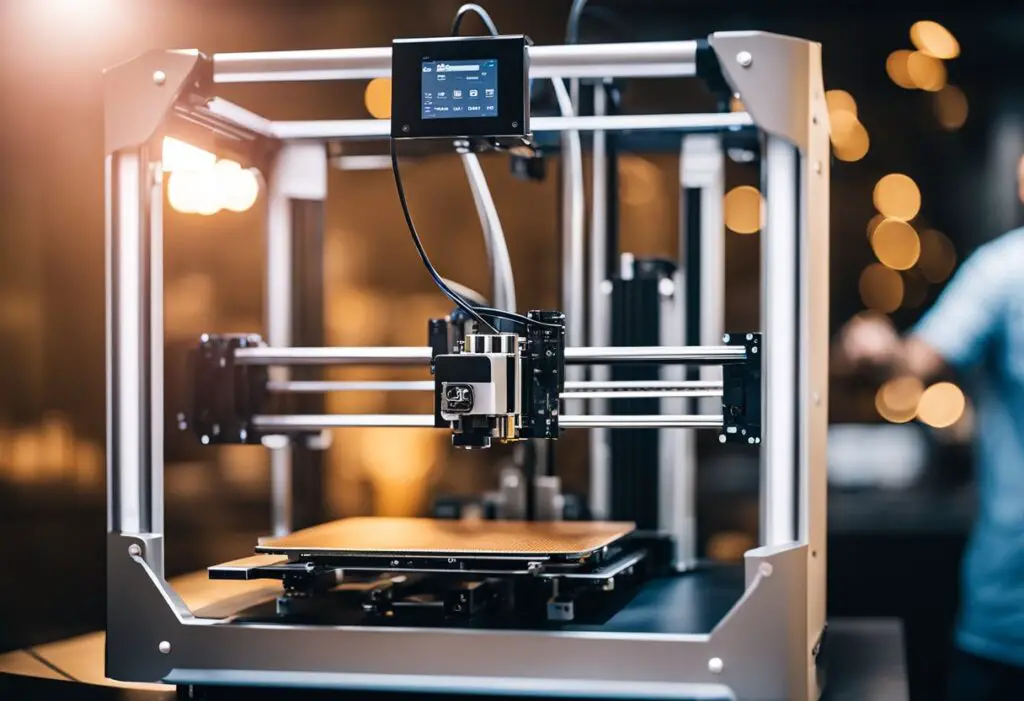
UART mode enables seamless data exchange between the printer’s control board and stepper motor drivers.
This communication allows for real-time adjustments to the stepper motor’s current, micro-stepping, and other vital parameters without requiring manual configuration or jumpers.
As a result, UART mode contributes to better precision and smoother operation of 3D printers, enhancing their overall performance.
Although UART is just one of several communication protocols used within the 3D printing realm, it has become increasingly popular due to its compatibility, efficiency, and flexibility.
As we explore further innovations in this rapidly advancing technology, methods like UART play a crucial role in elevating the quality, capabilities, and potential applications of 3D printing.
Understanding UART Mode in 3D Printing
UART mode is an essential aspect of 3D printing, as it stands for Universal Asynchronous Receiver/Transmitter.
It is a hardware component responsible for the transmission and reception of serial data between two devices. In 3D printing, UART mode plays a critical role in communicating with stepper motors and stepper drivers.
In 3D printers, UART mode enables the firmware to dynamically and actively control TMC2208-based SilentStepSticks (stepper motor drivers) through serial communication.
This control extends to various parameters, such as microsteps and driver current, which are essential for accurate and smooth movement in the 3D print process.
Some benefits of employing UART mode in 3D printing include:
- Enhanced control over stepper motor performance.
- Real-time adjustments to printing parameters.
- Ability to monitor and read status information from the stepper drivers.
In summary, UART mode in 3D printing dramatically improves print quality and efficiency by offering precise control and real-time communication between stepper motors and their drivers.
Components Involved
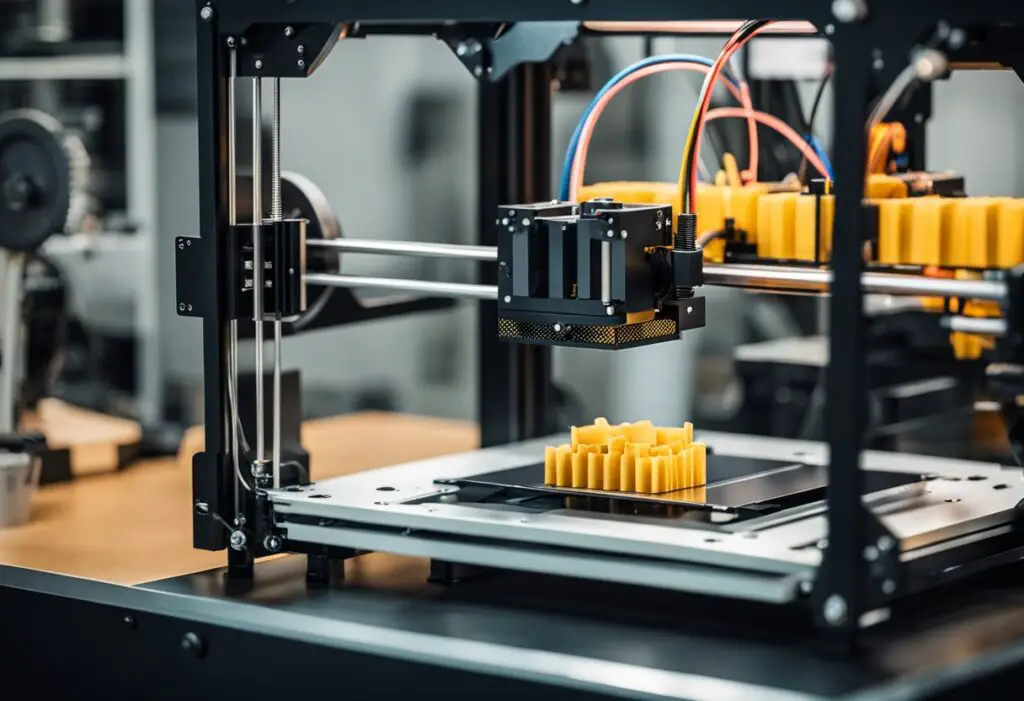
Stepper Motors
Stepper motors are an essential component of 3D printers, as they precisely control the movement of the printer’s axes.
These motors move in small, discrete steps or increments, providing accurate positioning and repeatability.
They operate by alternating magnetic fields between the rotor and the stator, creating a torque that results in the stepped motion.
There are different types of stepper motors, but most 3D printing applications use bipolar and unipolar motors.
Choosing a suitable stepper motor for your application depends on factors such as torque requirements, motor size, and operating voltage.
Driver Boards
Driver boards are responsible for controlling stepper motors in 3D printers. They receive signals from the main control board and amplify the current to deliver sufficient power to the stepper motor.
The driver board converts the signal into a series of micro-step commands, allowing the motor to move accurately.
Common driver boards used in 3D printers include the Trinamic TMC2208, Allegro A4988, and Texas Instruments DRV8825.
The drivers can be operated in different modes, such as UART and SPI, which determine how the driver boards communicate with the main control board.
Chip
The chips on the driver boards are the critical components in regulating the stepper motor’s motion.
They are responsible for processing the input signals, adjusting the current flow, and controlling the smooth rotation of the motor.
Chips like the TMC2208 allow the driver board to be controlled through UART mode, providing advanced features and dynamic control options for the stepper motor directly through the firmware Marlin in 3D printers.
Utilizing the right chip can enhance the overall performance and efficiency of your 3D printer.
When connecting these components, it is essential to use proper connectors to maintain reliable electrical connections.
Dupont connectors are commonly used for this task, allowing secure and standardized connections between the electronic components.
Overall, stepper motors, driver boards, and chips play critical roles in the performance and reliability of a 3D printer, ensuring utmost precision and control in the printing process.
The Role of Firmware
In 3D printing, firmware is crucial in controlling and managing various printer components.
One of the most popular open-source firmware is Marlin, which allows users to configure their 3D printer’s settings and optimize performance.
Two essential files within the Marlin firmware are configuration.h
and configuration_adv.h
.
These files contain numerous parameters that can be adjusted to customize the printer for specific needs. These adjustments can include settings related to the printer’s motion system, end stops, temperature control, etc.
A significant aspect of firmware, such as Marlin, is its ability to communicate and control various electronic components in a 3D printer.
In particular, it governs the stepper motors and their drivers, enabling the precise movements required for accurate prints.
UART mode is one communication method the firmware employs, allowing for more dynamic and active control of stepper motor drivers.
By configuring UART mode through the Marlin firmware, users can gain greater control and flexibility in their 3D printers’ performance.
This includes adjusting the motor’s current micro-steps and transitioning between different operation modes, such as stealthChop and spreadCycle, which control the noise levels and torque of the motors.
With the proper configuration and tuning of firmware settings, users can achieve optimal print quality and efficiency from their 3D printers.
In summary, the role of firmware, particularly Marlin, in 3D printing is indispensable.
Through the use of key configuration files and enabling advanced communication features like UART, firmware grants users the ability to fine-tune their 3D printers for improved performance and quality.
Diving into TMC2208 and TMC2209
TMC2208 Drivers
TMC2208 drivers are popular stepper motor drivers for 3D printers because of their quiet operation and advanced features.
They can be run in both UART and standalone modes. In standalone mode, you need to adjust the Vrefs manually with the potentiometer on each driver board, and it defaults to stealthchop2.
UART mode, on the other hand, allows for more control through firmware adjustments, such as Vrefs and stepping modes.
To switch TMC2208 from standalone to UART mode, a resistor may be required to bridge specific pads on the driver board.
This enables serial communication with the mainboard for dynamic control through firmware, such as Marlin.
TMC2209 Drivers
TMC2209 drivers are an upgraded version of the TMC2208, offering more power and additional features. They also differ in heat dissipation, and their performance is better optimized for specific 3D printer models.
Just like their predecessor, TMC2209 drivers support UART communication, allowing the user to seamlessly adjust the current, micro-stepping mode and other settings through G-code commands.
This eliminates the need for manual Vref adjustments and simplifies configuring and maintaining a 3D printer.
By using TMC2208 or TMC2209 drivers, 3D printer enthusiasts can achieve quieter and more efficient operation for their machines and have more control over their printing process.
UART Mode Configurations
UART mode in 3D printing allows for enhanced communication between the stepper motor drivers and the printer’s motherboard.
This mode enables dynamic control of motor current, microsteps, and other settings, offering a more efficient and precise printing experience.
To implement UART mode, it is necessary to set up the motherboard and stepper motor drivers accordingly. Common drivers used in 3D printers, such as the A4988, may require hardware modifications before enabling UART mode.
This typically involves soldering connections on the driver board or altering settings within the firmware.
One significant advantage of UART mode over other communication protocols is the ability to control microsteps, which can improve the accuracy and smoothness of your printer’s movements.
Microstepping is the process of dividing each full step of the motor into smaller, more precise steps.
To configure this feature, VREF (voltage reference) settings on the stepper motor driver must be adjusted, either manually or through software control.
Connecting your stepper motor drivers to the motherboard in UART mode may require adjusting the PDN (Power Down) signal settings.
The PDN signal is used to manage power and disable the stepper motors when necessary.
Sometimes, the same pin on the stepper motor driver receives serial data when operating in UART mode, enabling advanced features like homing without limit switches or sensing obstructions.
When configuring UART mode in 3D printing, it is essential to ensure compatibility between the stepper motor drivers and the motherboard, as they must work closely together for optimal performance.
Additionally, the firmware should support UART mode to take full advantage of the benefits offered.
In conclusion, UART mode configurations in 3D printing provide more precise control over the printer’s movements, enabling advanced features and improved accuracy.
By appropriately setting up your stepper motor drivers and motherboard and adjusting the necessary settings, you can optimize your 3D printing experience.
Commercial Support and Advantages
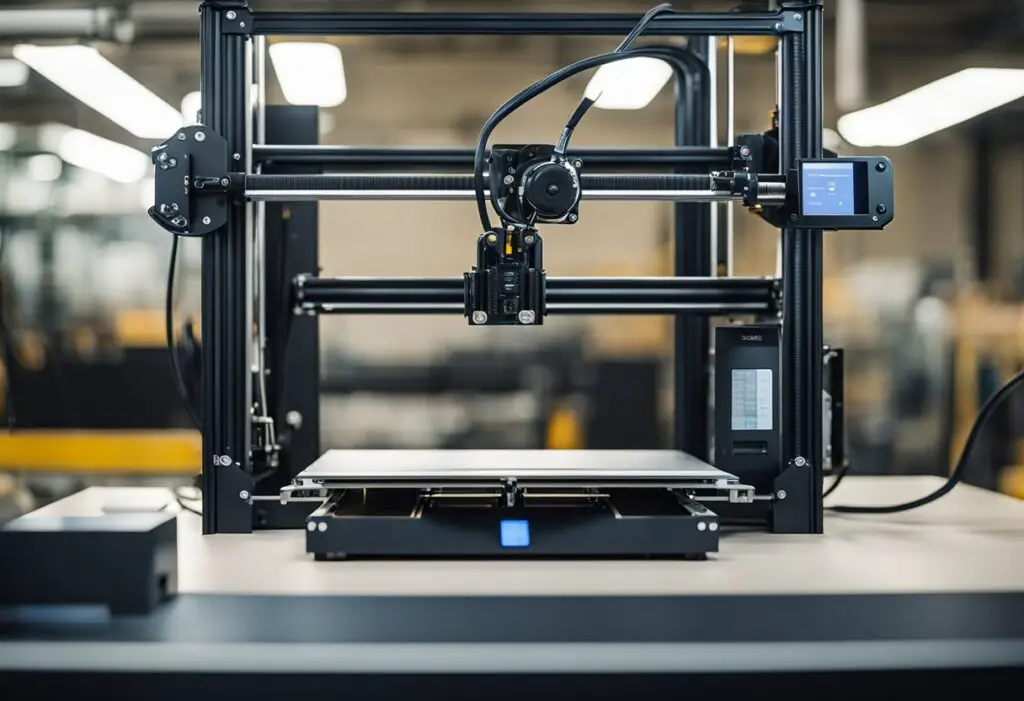
Many 3D printer manufacturers and the open-source community support UART mode for stepper motor drivers.
This creates an ecosystem that allows users to access resources and experience the benefits of UART mode easily.
One major advantage of UART mode is the high level of control it provides.
Thanks to the two-way communication between the stepper motor driver and the microcontroller, it enables users to fine-tune settings such as motor current, speed, and torque.
This results in smoother, quieter, and more accurate 3D printing experiences.
In addition, the UART mode allows for dynamic torque adjustment.
This means that the stepper motor can automatically adjust torque based on the demands of the printing job, leading to improved efficiency and reduced wear on the motors.
Another aspect worth mentioning is the ease of configuration and updating for UART-based stepper drivers.
Due to its connection with the main microcontroller, updating firmware or tweaking settings becomes much more straightforward.
This can save time, reduce frustration, and help hobbyists and professionals create better 3D-printed projects.
In conclusion, the commercial support for UART mode in 3D printing offers several advantages, including better control over stepper motors, increased torque management capabilities, and a more user-friendly configuration experience.
These benefits contribute to a higher-quality, more efficient 3D printing process.
Working with Datasheets and Pinouts
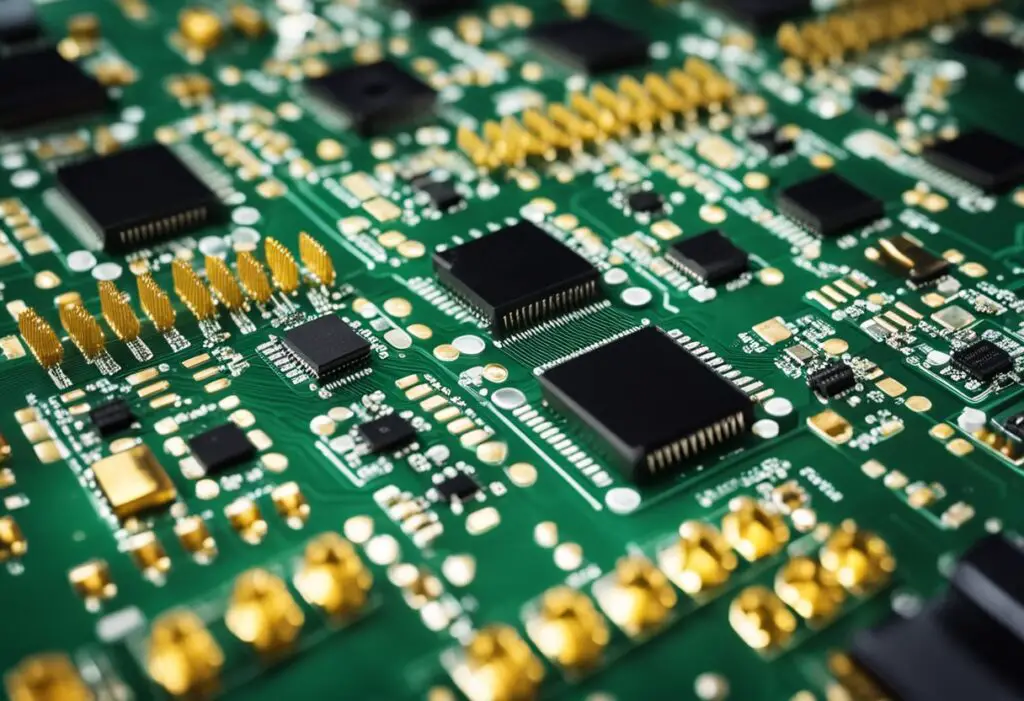
When working on a 3D printing project that involves UART mode, it’s essential to become familiar with datasheets and pinouts.
Datasheets provide detailed information about a component’s specifications, functions, and capabilities, while pinouts depict how a component’s pins should be connected.
The first step is to consult the datasheet of the UART device being used for the 3D printer. This document helps you understand the device’s features, modes of operation, and performance characteristics.
Additionally, it may provide information about software configuration options and packet structure, which are essential when working with UART interfaces.
Next, you must familiarize yourself with the pinouts of the UART device. Pinouts are visual representations of a device’s pins and functions, usually available within the datasheet or a separate document.
Understanding the pin connections is crucial to ensure proper functionality and communication between the UART device and the 3D printer’s main controller board.
When connecting the UART device to the 3D printer, remember to pay close attention to the pinout diagram.
Misconnecting pins may result in faulty operation or permanent damage to the component. Always double-check your connections before powering the printer to avoid any unexpected issues.
In conclusion, when working with UART mode in 3D printing, it’s essential to study datasheets and pinouts carefully.
Proper interpretation and application of this information will ensure successfully integrating UART devices into your project, ultimately enhancing your 3D printer’s capabilities and performance.
The Role of StealthChop Mode and SpreadCycle Mode
StealthChop and SpreadCycle are two modes for controlling stepper motor drivers in 3D printers, especially those using Trinamic TMC drivers.
These modes are essential for achieving the desired performance in various 3D printing operations.
StealthChop mode uses PWM voltage to drive the motors quietly and smoothly, making it nearly inaudible during low-speed operations.
This mode is highly advantageous for detailed and delicate printing tasks, as it reduces noise levels and ensures smooth operation. However, it has a lower stepping speed limit, which may not be suitable for fast travel moves.
On the other hand, SpreadCycle mode is a more robust and dynamic mode designed for higher-speed operations. It uses a current-based approach to drive the motors, providing higher precision at higher speeds.
This mode is typically used for fast travel moves and other high-speed tasks that require rapid motor response.
To switch between the two modes, G-code commands can be used, allowing users to easily toggle between StealthChop and SpreadCycle modes during the printing process.
For example, the TMC drivers can be configured using the “stealthchop_threshold” parameter.
Motor current is an important aspect when choosing between StealthChop and SpreadCycle modes. StealthChop’s PWM voltage-based approach can result in lower motor current, which is beneficial in power-sensitive applications.
Meanwhile, SpreadCycle’s current-based control provides better regulation of motor current, ensuring consistent performance at higher speeds.
In summary, StealthChop mode is best for low-speed, quiet operations and delicate prints, whereas SpreadCycle mode is suitable for high-speed printing and rapid travel moves.
Users can configure their 3D printers to switch between these modes with G-code commands and consider motor current to optimize performance in different printing scenarios.
Heat Management
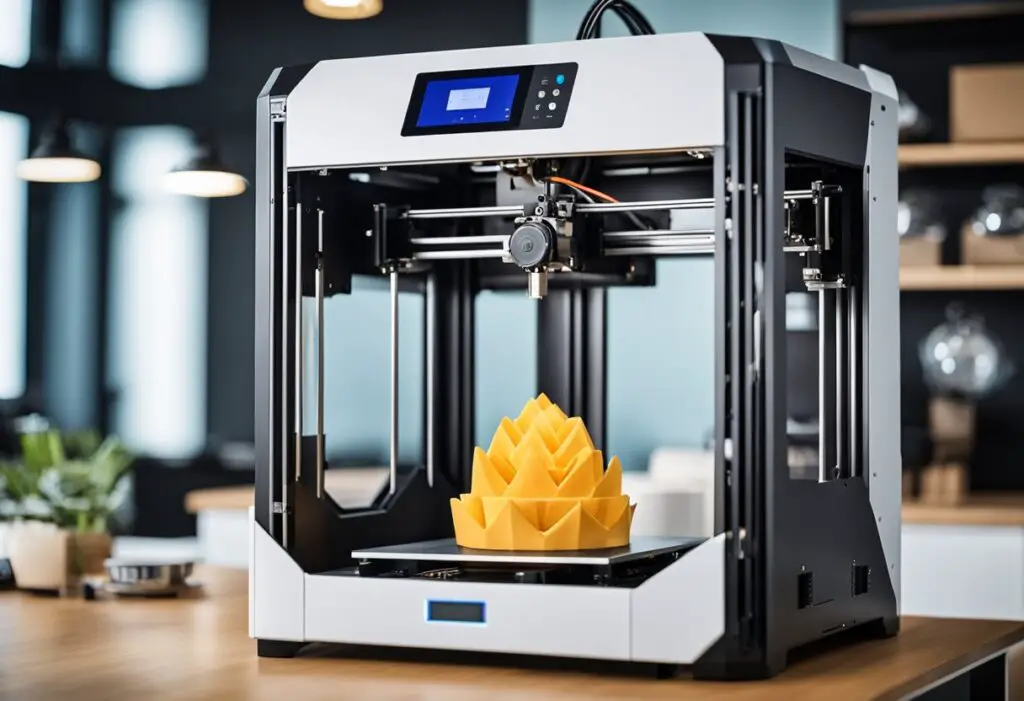
Heat management, specifically in 3D printing, is vital in ensuring optimal printing quality and mitigating potential printing issues.
As the stepper motors generate heat during operation, it is essential to maintain adequate temperature control to prevent overheating.
One effective heat management tool for stepper motors is the use of heatsinks. Heatsinks are usually made of thermally conductive materials like aluminum or copper and are designed to dissipate heat effectively away from the motors.
By attaching heatsinks to the stepper motors, their temperature remains controlled, reducing the risk of motor malfunction or damage.
Moreover, controlling the current supplied to the stepper motors is essential in maintaining a proper heat management system.
Motors with higher currents tend to generate more heat, which can lead to overheating.
To avoid this, it is crucial to adjust the current settings in the firmware or opt for lower current stepper drivers to maintain an appropriate balance between motor performance and thermal management.
Incorporating these heat management techniques in UART mode 3D printing ensures the longevity of the printer and the quality of its prints while minimizing the risk of potential issues related to overheating.
By being mindful of the significance of heat management, a 3D printer user can achieve better results in their printing projects.
Further Steps
When utilizing UART mode in 3D printing, taking the proper further steps ensures smooth operation and enhanced performance.
One of the most important aspects of UART mode is understanding the role of stepper drivers and the communication between these drivers and main control boards through specific pins.
In UART mode, each stepper driver has dedicated step and direction pins. This mode allows customizations by enabling dynamic control of various settings directly through the firmware.
Users can adjust motor currents and micro-steps while benefiting from advanced features such as diagnostics, obstruction sensing, and limit switch-free homing.
To make the most of UART mode, it is essential to configure the firmware correctly. Popular firmware choices, such as Marlin, offer comprehensive documentation detailing the necessary adjustments in the firmware to enable UART functionality.
Additionally, this requires the appropriate wiring or soldering of the UART pin on the stepper driver to the corresponding pins on the control board.
For those looking to expand their 3D printing capabilities, diving deeper into the possibilities unlocked by UART mode will result in improved motor control and added functionality.
Learning about stepper drivers and their corresponding pins and configuring firmware are crucial steps in this journey.
By familiarizing oneself with the numerous resources available, users can achieve optimal 3D printing results while enjoying the advantages of UART mode.
Selected Hardware: SKR v1.3 and BIQU
The SKR v1.3, developed by BIGTREE-TECH, is a popular choice for 3D printing enthusiasts looking to upgrade their hardware.
It’s known for its enhanced performance, thanks to the 32-bit processing power, which significantly improves the overall printing experience.
This mainboard can be set up swiftly using a step-by-step guide for easy installation.
BIQU, an associated brand of BIGTREE-TECH, collaborates in producing quality components compatible with SKR v1.3.
One such component is the TMC2208 driver module, which operates in UART mode and allows for enhanced control over your 3D printer.
The TMC2208 module is designed to offer precise and smooth motor operations while reducing noise levels.
To set up the TMC2208 with SKR v1.3 in UART mode, you can follow an online tutorial, which provides detailed instructions for configuring the hardware with Marlin.
In addition to the TMC2208 module, BIQU also offers the TFT35 v3 display, which could be integrated into the SKR v1.3 hardware setup for easier monitoring and control of your 3D printer.
This full-color touchscreen complements the UART setup and provides a user-friendly interface for changing settings and monitoring the printing progress.
A comprehensive video tutorial on setting up the SKR v1.3 with the TFT35 v3 display can be found here.
By choosing the SKR v1.3 mainboard and incorporating components like the TMC2208 and TFT35 v3, users can enhance their 3D printing experience.
These upgrades improve control, precision, and user interface, translating into better final prints. Just remember to follow the instructions provided in the various tutorials closely for optimal results.
Working with Text Editor and Drivers
When working with 3D printing and UART mode, it’s important to use a text editor for modifying firmware settings, such as the e0_driver_type
and e0_rsense
.
A text editor is a software application that enables you to write, edit, and save plain text files. Examples of popular text editors include Notepad++, Sublime Text, and Visual Studio Code.
The e0_driver_type
is a setting in the firmware that defines the type of stepper motor driver used for the extruder 0 (E0) motor.
Different drivers have different capabilities and require different settings in the firmware for optimal performance and control.
To configure the stepper driver in UART mode, you must adjust the settings in the text editor. For example, if you are using the TMC2208 driver, you would set the e0_driver_type
to TMC2208
.
The e0_rsense
refers to the sense resistor value for the extruder 0 motor driver. The driver manufacturer typically specifies this setting and usually has a default value.
In some cases, you might have to adjust the e0_rsense
value to match the specific hardware configuration of your 3D printer. This value helps the driver determine the correct current for the stepper motor, ensuring precise and efficient operation.
When working with text editors and drivers, save any changes you make to the firmware settings.
Once your settings are modified and saved, you can upload the new firmware to your 3D printer’s control board for smooth and efficient UART mode operation.
Using a suitable text editor and configuring the drivers properly will help you get the most out of your 3D printer and ensure optimal performance and quality in your printed objects.
Transitioning from SPI to UART Mode
Transitioning from SPI to UART mode in 3D printing involves changing the communication protocol between the printer’s control board and stepper motor drivers.
Both SPI and UART are communication protocols that enable the control board to send commands and receive feedback from the motor drivers. However, they differ in their working principles and implementation.
One of the main benefits of using UART mode over SPI in 3D printing is the ability to dynamically set stepper motor current, microstepping, and other settings through software rather than relying on physical jumpers.
This allows for more precise control and potentially smoother print results. Additionally, UART mode can offer a lower noise performance, which may benefit printers operating in quiet environments.
To transition from SPI to UART mode, the first step is to ensure that the stepper motor drivers support UART communication.
Many popular stepper drivers, such as those based on the Trinamic TMC series, support both protocols, making the switch relatively straightforward.
Before making any changes, it is essential to power off the 3D printer and prepare the necessary tools and software.
Once the printer is powered off, you may need to remove or reconfigure the jumpers on the control board to enable UART mode.
Refer to the specific board’s documentation for instructions on jumper settings and wiring. Remember that each driver may need to be wired differently, and it is crucial to follow the manufacturer’s guidelines to avoid damaging the components.
After adjusting the hardware, modify the firmware configuration to enable UART communication.
This may involve updating the firmware source code to reflect the new communication protocol and recompiling it.
Ensure that all relevant settings, such as motor current and micro-stepping, are correctly configured to take advantage of UART’s dynamic control capabilities.
Finally, upload the modified firmware to the printer’s control board, ensuring a successful transition from SPI to UART mode. After rebooting the printer, monitor its performance and fine-tune the settings to achieve optimal printing results.
Exploring TMC5160
The TMC5160 is a powerful and versatile stepper motor driver designed specifically for high-performance applications, such as 3D printing.
One of the critical features of the TMC5160 is its ability to operate in UART mode, enabling smoother and quieter operation of the stepper motors compared to traditional step and direction motor drivers.
UART mode, or Universal Asynchronous Receiver/Transmitter mode, allows for real-time communication between the motor driver and the controller board, making it easier to adjust settings like current, microstep resolution, and other advanced driver options on the fly.
This feature ensures the best performance and efficiency from your 3D printer’s stepper motors, resulting in improved print quality and a more enjoyable user experience.
In addition to UART compatibility, the TMC5160 boasts many other beneficial features.
For instance, it supports SPI communication, providing high-speed, bidirectional data transfer between the motor driver and controller board.
This allows for even more advanced configuration options and offers even better motor performance for demanding applications.
Another advantage of the TMC5160 is its ability to utilize stealthChop™ and spreadCycle™ technologies, which help to minimize motor noise and vibration.
These features, combined with the UART communication mode, create a seamless and reliable control solution for your 3D printer.
To wrap it up, the TMC5160 stepper motor driver offers advanced features and ease of use, making it an excellent choice for enhancing the 3D printing experience.
By embracing UART mode and leveraging the full capabilities of this motor driver, you can experience smoother, quieter, and more efficient operation for your 3D printer.