3D printing has revolutionized the manufacturing industry, allowing for the production of complex and diverse objects with increased efficiency.
One key element that makes 3D printing possible is the use of various types of plastics as the primary building material.
With such a wide range of applications, it’s essential to understand the kind of plastic used in 3D printing which possesses different properties tailored to specific needs.
The most common plastics used for 3D printing include Acrylonitrile Butadiene Styrene (ABS) and Polylactic Acid (PLA).
While ABS is known for its durability, strength, and heat resistance, making it popular in automotive and electronic industries, PLA is a biodegradable plastic derived from renewable sources like corn starch, boasting a low melting point and solid strength, ideal for lightweight and consumer applications.
As the 3D printing industry continues to grow, the variety of plastics will only expand, enabling greater possibilities and further innovation.
Understanding the characteristics of these plastics is crucial for designers, engineers, and enthusiasts alike in leveraging this transformative technology effectively.
Table of Contents
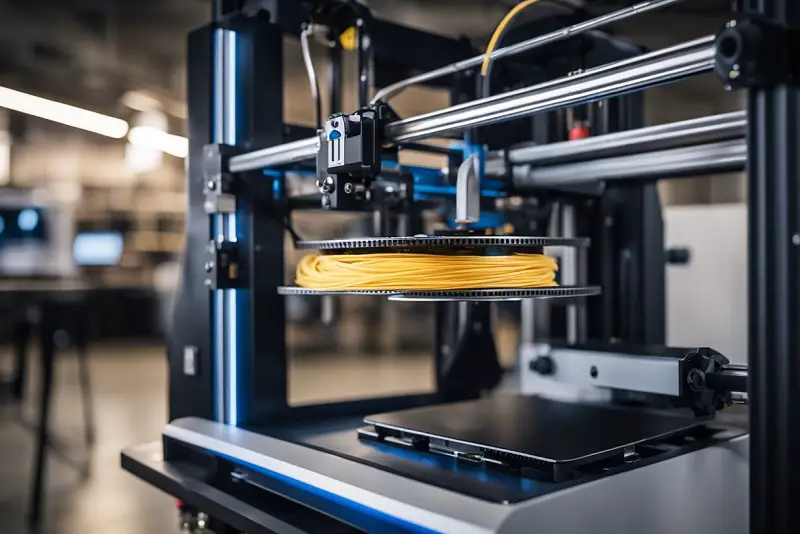
Types of Plastic Used in 3D Printing
ABS (Acrylonitrile Butadiene Styrene)
ABS is one of the most commonly used plastics in 3D printing, particularly for industrial applications.
It is strong, durable, and resistant to high temperatures. ABS is available in various colors and finishes, making it suitable for a wide range of products.
Pros:
- Strong and durable
- Temperature resistance
- Widely available
Cons:
- Requires a heated print bed
- May produce toxic fumes during printing
PLA (Polylactic Acid)
PLA is a popular choice for non-industrial 3D printing due to its ease of use and eco-friendly nature.
Made from renewable resources, PLA can be used in both resin and filament form and offers an extensive range of colors.
Pros:
- Eco-friendly
- Easy to print with
- Available in various colors
Cons:
- Less durable than other plastics
- Not temperature resistant
PET (Polyethylene Terephthalate)
PET and its variants, such as PETT and PETG, are popular 3D printing plastics due to their strength, flexibility, and chemical resistance.
PET is commonly used for food-safe applications and packaging.
Pros:
- Food-safe
- Strong and flexible
- Chemical resistant
Cons:
- Less temperature resistant compared to ABS
- May require a heated bed for printing
Nylon
Nylon is a very versatile plastic, favored for its strength, durability, and flexibility.
This plastic is commonly used in industrial applications, automotive parts, and medical devices.
Pros:
- Strong and flexible
- Suitable for various applications
- Chemically resistant
Cons:
- Hygroscopic, absorbs moisture from the air
- May require a heated bed and enclosure
ASA
ASA (Acrylonitrile Styrene Acrylate) is similar to ABS but has improved resistance to UV light, making it a popular choice for outdoor applications.
Pros:
- UV-resistant
- Strong and durable
- Weatherproof
Cons:
- More difficult to print with compared to PLA
- Requires a heated bed and enclosure
PP (Polypropylene)
PP is known for its chemical resistance and flexibility. It’s commonly used for packaging, automotive parts, and chemical containers.
However, PP can be challenging to 3D print due to its low surface energy and warping tendencies.
Pros:
- Chemical resistant
- Flexible and durable
- Food-safe
Cons:
- Difficult to print with
- Requires specialized printing techniques
PVA (Polyvinyl Alcohol)
PVA is a water-soluble plastic that is primarily used as a support material in 3D printing. It dissolves in water, allowing for easy removal of complex support structures after printing.
Pros:
- Water-soluble
- Easy support material removal
- Compatible with other plastics
Cons:
- Not suitable for structural applications
- Hygroscopic, sensitive to moisture during storage
HIPS (High Impact Polystyrene)
HIPS is a lightweight and versatile material that is easy to print with. It can be used as a support material or as a standalone material for creating lightweight and rigid parts.
Pros:
- Lightweight and rigid
- Easy to print with
- Can be used for support material
Cons:
- Less durable compared to other plastics
- Not suitable for high-temperature applications
Properties of Different 3D Printing Plastics
Strength and Durability
3D printing plastics exhibit a range of strength and durability properties. Strong materials, such as nylon, are known for their exceptional toughness and impact resistance, making them ideal for mechanical applications and moving parts.
Many 3D printing plastics also display impressive durability, able to withstand daily wear and tear.
This makes them suitable for producing long-lasting objects, from everyday household items to industrial components.
Flexibility
Flexibility is another key property of certain 3D printing plastics. Materials like thermoplastic polyurethane (TPU) or flexible PLA offer a higher degree of flexibility compared to traditional plastics, allowing them to bend and twist without breaking.
This characteristic is useful in applications where items need to adapt to external pressure or conform to specific shapes, such as gaskets, seals, and wearable devices.
Temperature Resistance
Some 3D printing plastics are specifically designed to withstand high temperatures, making them suitable for applications in environments where other materials might fail.
For example, materials like polyetherimide (PEI) and polyphenylsulfone (PPSU) can maintain their structural integrity in temperatures exceeding 200°C.
This temperature resistance is particularly valuable in industries such as automotive, aerospace, and electronics, where components may be exposed to extreme temperature fluctuations.
Environmental Impact
The environmental impact of 3D printing plastics varies, with some materials being more eco-friendly than others.
Biodegradable materials like polylactic acid (PLA) are derived from renewable sources, making them a sustainable choice for 3D printing. PLA’s ability to degrade naturally over time also helps to reduce its environmental footprint.
On the other hand, some plastics, such as ABS, may not be as environmentally friendly due to their reliance on fossil fuels for production and their slower decomposition rates.
When selecting a 3D printing plastic, it’s essential to consider the environmental impact alongside factors like strength, flexibility, and temperature resistance.
Emerging Materials in 3D Printing
Composites and Fiber-reinforced Plastics
Composites and fiber-reinforced plastics are gaining popularity in the 3D printing industry due to their enhanced strength and durability.
One such composite is carbon fiber, which is a lightweight material that offers high tensile strength.
When combined with thermoplastics like PLA or ABS, these composites result in strong and lightweight 3D printed components that are ideal for applications in industries such as aerospace and automotive.
Aside from carbon fiber, other fibers like glass and aramid are also being incorporated into 3D printing materials to improve their mechanical properties.
These fiber-reinforced plastics provide added strength, stiffness, and resistance to wear and tear.
Metal-filled Plastics
Metal-filled plastics are innovative 3D printing materials that blend metal particles, such as aluminum, with traditional thermoplastic resins.
This combination provides the printed parts with a unique metallic appearance and increased weight, while still maintaining the ease of printing associated with plastic materials.
Metal-filled plastics can be post-processed, polished, or even subjected to specific treatments to achieve a near-real metal appearance, making them useful for producing decorative items, jewelry, and prototypes.
Specialty Filaments
Recent advancements in 3D printing materials have led to the development of specialty filaments that cater to specific applications and industries.
Some of these innovative materials include wood-filled plastics, which consist of a blend of plastic and finely ground wood particles, mimicking the texture and appearance of real wood.
Wood-filled plastics can be sanded and stained like traditional wood, making them popular for creating artistic pieces or furniture components.
Other specialty filaments include transparent and optical materials, which can be utilized to create clear or light-diffusing components, such as light covers or lenses.
With these unique materials, 3D printing continues to push boundaries in terms of design capabilities and expand its applications across various industries.