3D printing has revolutionized numerous industries, and one of the most notable advancements is in the field of construction with the advent of concrete 3D printing.
Also known as additive manufacturing, this technology enables the creation of complex structures while significantly reducing material waste and offering a more sustainable construction solution.
As this innovative method gains traction, it becomes essential to understand the types of concrete utilized for 3D printing.
The key to successful concrete 3D printing lies in the unique blend of materials, ensuring both structural properties and printability.
This typically involves specialized mixes of cementitious materials, aggregates, and admixtures tailored to the specific printing process.
Researchers have experimented with various combinations to enhance the mechanical performance of 3D-printed concrete, including the use of recycled sand and other unconventional substitutes.
In the world of additive manufacturing, the choice of concrete greatly impacts the final product, and the ongoing advancements in material science and 3D printing technology show promising potential for the future of eco-friendly and innovative construction methods.
Table of Contents
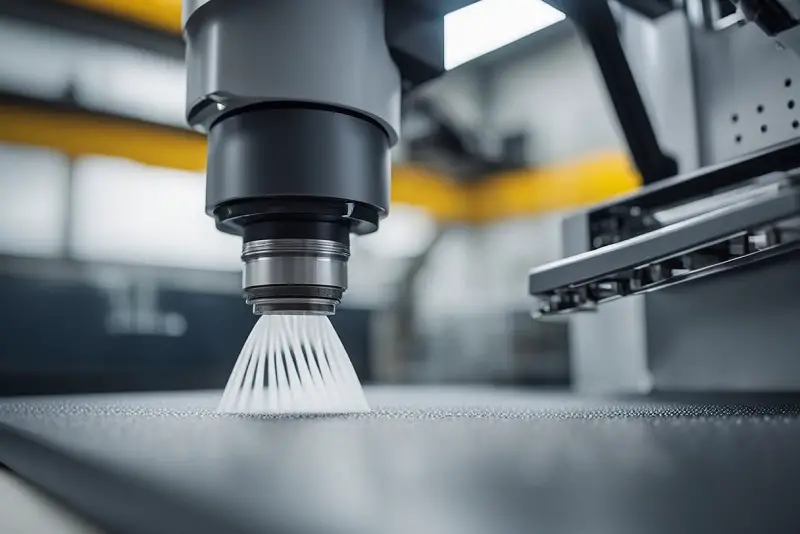
Overview of 3D Concrete Printing
3D concrete printing is an innovative technology that has the potential to transform the construction industry.
By combining additive manufacturing techniques with cementitious materials, this method offers a faster, cheaper, and more sustainable alternative to traditional building methods.
The use of concrete 3D printers, materials, and various printing processes ensures a versatile solution for producing complex and customized designs.
There are two main types of concrete printers used in the industry: gantry concrete 3D printers and robotic arm printers.
Gantry printers excel in large-scale projects and have the benefit of easier programming, while robotic arms offer precision and portability, albeit with some limitations in scaling up.
Depending on project requirements, builders can select the most suitable type of 3D printer to optimize construction efficiency.
When it comes to 3D printing concrete, the process typically involves extruding layers of cementitious material or real concrete in a precise and controlled manner.
This allows for complex geometries and designs that would be difficult or impossible to achieve using conventional construction methods.
Furthermore, 3D-printed concrete structures are often stronger and more durable than their traditional counterparts, given the ability to optimize the material properties and composition.
Beyond its applications in the construction industry, 3D concrete printing has also found its way into various infrastructure projects, such as water management, bridges, and railways.
As this technology continues to develop and mature, the potential for widespread adoption and a significant impact on the built environment is becoming increasingly evident.
By embracing the power of 3D printing concrete, industries are not only improving construction efficiency but also promoting sustainable practices and reducing the overall environmental impact.
As a result, 3D concrete printing is poised to redefine the future of building and infrastructure design in the years to come.
Materials Used in 3D Concrete Printing
Concrete Mix
The concrete mix used for 3D printing is crucial for the success of the project. The mix should have an optimum balance of flowability, buildability, and strength.
3D-printed concrete typically has a higher content of cementitious materials, which allows for better bonding between layers and improved self-supporting capabilities.
The mix design may also include various additives to control the setting time and improve the structural properties of the printed concrete.
Cementitious Materials
In 3D concrete printing, cementitious materials play a vital role in forming strong, resilient structures.
There are various types of cementitious materials that can be used, including ordinary Portland cement (OPC), fly ash, and ground granulated blast furnace slag (GGBS).
Some sustainable materials such as low-carbon binders and low-energy binders are becoming increasingly popular in 3D concrete printing due to their reduced environmental impact.
Aggregate and Particle Size
Aggregate selection is crucial in determining the properties of the 3D-printed concrete. Aggregates used in conventional concrete are typically replaced by finer particles in 3D printing concrete mix designs.
This change in particle size distribution helps maintain a smooth, uniform extrusion during the printing process.
The use of recycled materials, such as crumb rubber and polypropylene fibers, is also being explored to enhance the performance and sustainability of 3D-printed concrete.
Water and Hydration
Water is essential in the 3D concrete printing process, as hydration is a key factor that determines the mechanical performance of the printed structures.
The water-to-cement ratio (w/c ratio) controls the rate of hydration, impacting the stiffness and strength of the printed concrete.
In 3D printing, a lower w/c ratio is often used to reduce deformation and improve layer adhesion.
However, this can affect the workability of the mix, highlighting the importance of finding an optimal balance for water and hydration.
Properties of 3D Printed Concrete
Fresh Properties
3D-printed concrete shows unique fresh properties that distinguish it from traditional concrete. These properties include flowability, workability, and pumpability, which are crucial for the extrusion process during printing.
Flowability ensures the smooth movement of concrete through the nozzle, while workability refers to the concrete’s ability to be easily compacted without segregation.
Pumpability, on the other hand, defines how readily the concrete can be transported through the printing equipment.
Hardened Properties
Hardened properties are essential in determining the performance and durability of 3D-printed concrete structures.
Attributes like compressive strength and porosity influence the material’s ability to bear loads and resist weathering.
The use of supplementary cementitious materials (SCMs), such as fly ash or silica fume, can enhance the concrete’s microstructure and improve its hardened properties.
Rheological Properties
In the realm of 3D-printed concrete, rheological properties play a vital role in ensuring the structural integrity of printed objects.
Three primary rheological properties are considered for 3D printing: extrudability, shape retention, and anisotropy.
Extrudability refers to the concrete’s ability to be extruded smoothly through the nozzle, while shape retention reflects its capacity to maintain its form after printing. Anisotropy deals with the variations in mechanical properties within the 3D-printed object, ensuring the printed layers bond correctly and provide adequate stability.
When it comes to selecting the type of concrete for 3D printing, a sustainable option is often preferred. Utilizing Portland cement as a binder, the addition of SCMs contributes to the material’s sustainability by reducing the cement content.
Besides boosting the concrete’s performance, these additions aid in lowering the undesirable environmental influences of concrete production.
In summary, 3D-printed concrete should exhibit both suitable fresh and hardened properties, as well as appropriate rheological characteristics to ensure the best performance for construction applications.
Taking these properties into account, researchers and professionals can select the ideal concrete for 3D printing within their specific projects and requirements.
Advantages and Disadvantages of 3D Concrete Materials
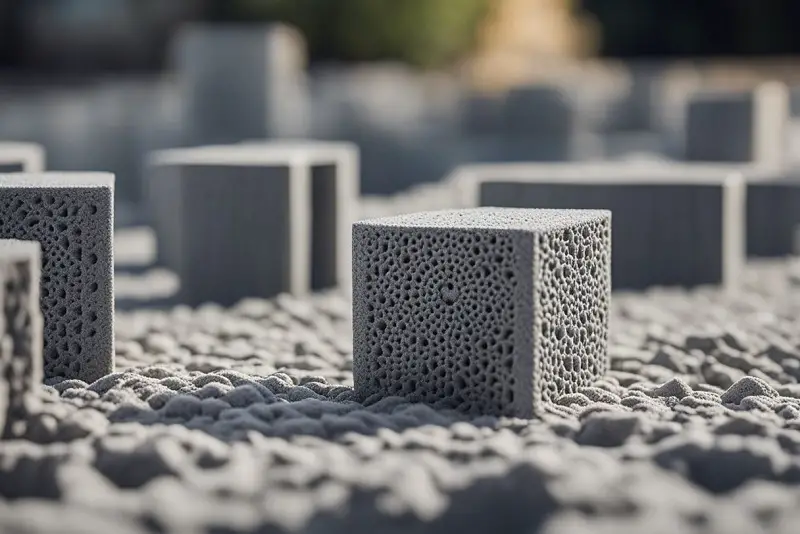
3D-Printed Concrete Advantages over Traditional Concrete Construction
One of its main benefits is the ability to create complex geometries and design freedom, which allows architects and engineers to develop intricate structures with ease.
Moreover, 3D concrete printing is a more sustainable option, as it reduces material waste and has a smaller carbon footprint compared to traditional methods.
Gantry systems and robotic arm systems are two primary types of concrete 3D printing technologies.
Gantry printers are suitable for large-scale projects due to their ease of programming, while robotic arms provide portability and precision, although they have limitations in scaling up.
Disadvantages associated with 3D-Printed Concrete
First, the technology is still in its developmental stages, meaning that its performance and applications have not yet been fully explored or optimized.
For instance, researchers are still working on refining the workability and mechanical properties of 3D-printed concrete.
Additionally, there can be challenges in achieving good bonding between layers, as well as setting the optimal printing time for 3D-printed concrete projects.
These factors can have an impact on the overall structural integrity and durability of the final product.
In conclusion, 3D-printed concrete has the potential to revolutionize the construction industry with its innovative design capabilities, sustainability, and improved efficiency.
However, further research and development are necessary to address the challenges and limitations currently associated with this emerging technology.