3D printing has revolutionized the way we create objects, from small household items to complex prototypes and parts for various industries.
As technology advances, more people are embracing 3D printing to bring their ideas to life.
For beginners and experienced professionals alike, it’s crucial to understand the essential equipment required for a successful 3D printing experience.
The core of any 3D printing setup is, of course, the 3D printer itself. However, several other tools and accessories play a vital role in the printing process.
From computers with suitable specifications that can handle 3D design and slicing software to consumables like filament, there’s more to 3D printing than just the printer.
Moreover, proper maintenance and post-processing equipment are essential to ensure that your 3D prints come out looking their best.
In this article, we’ll explore the various equipment that is needed for 3D printing, from basic tools to more advanced gadgets.
Whether you’re a beginner or a professional, having the right equipment can make all the difference in your 3D printing journey.
Table of Contents
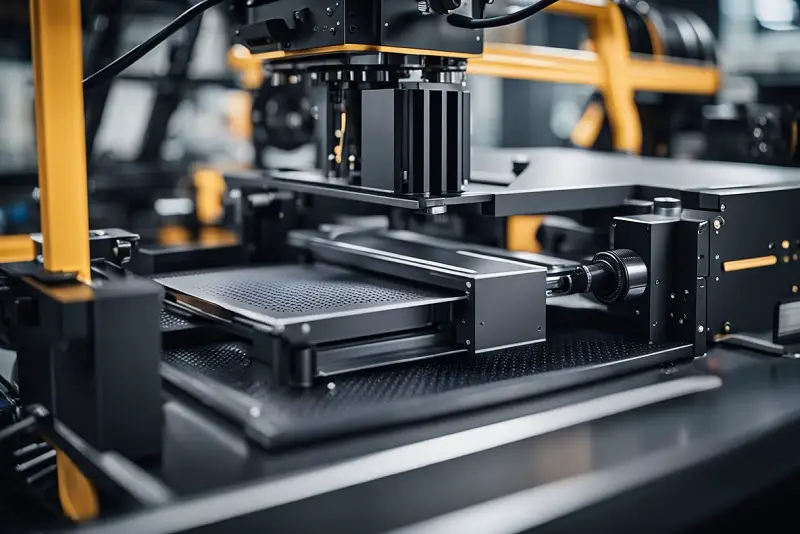
3D Printer Types and Selection
There are several different types of 3D printers available in the market. Two common types that consumers often opt for are the Cartesian printers, which further have Prusa-style (Cartesian XZ) and Ultimaker-style (Cartesian XY) formats, and Delta printers.
The choice between these 3D printers depends on your specific needs, budget, and the limitations of each type.
Fused deposition modeling (FDM) and stereolithography (SLA) are also popular 3D printing technologies.
FDM printers, like Ender 3 and Creality, use thermoplastic filaments that melt and solidify to create the desired object. SLA printers work with liquid resin and UV light to harden the material layer by layer.
Resin 3D printers usually offer better resolutions and smoother finishes than FDM printers.
Selecting the right 3D printer type depends both on your requirements and budget constraints. You might consider some factors like print quality, speed, and material compatibility.
For beginners and hobbyists, affordable FDM printers, such as Ender 3 and Creality, might be a good starting point.
However, for professionals who require high-quality prints with detailed accuracy, resin 3D printers or even other advanced technologies, such as selective laser sintering (SLS) or material jetting (MJ) could be the better choice.
These pro-level printers generally come with a higher price tag but are well-suited to deliver high-performance results.
Remember that each type of 3D printer comes with its limitations, so being aware of the capabilities and constraints can help you make the right decision for your 3D printing needs.
Essential Printing Materials
3D printing involves using a range of materials for different projects. Some common types include PLA, ABS, filament, resin, and photopolymer resin.
Each of these materials has its unique properties and applications, which directly impact the quality, durability, and functionality of the printed objects.
PLA (Polylactic Acid) is an eco-friendly, biodegradable thermoplastic derived from renewable resources such as corn starch and sugarcane.
PLA is ideal for beginners and hobbyists because it is easy to print with and has low warping tendencies. It’s commonly used for creating prototypes, educational models, and household items.
On the other hand, ABS (Acrylonitrile Butadiene Styrene) is a popular thermoplastic for more advanced users, due to its strength and resistance to high temperatures.
ABS can be used for making functional parts, enclosures, and automotive components, but it requires a heated bed and might produce unpleasant fumes during printing.
Filament-based 3D printing, like PLA and ABS, involves the use of spooled thermoplastic material that gets extruded through a hot nozzle onto the print bed.
These filaments come in various colors and thicknesses to suit different printers and applications.
Resin-based 3D printing, on the other hand, involves the use of liquid photopolymer resins that get cured by ultraviolet (UV) light.
These resins allow for high-detail printing and are ideal for creating intricate models, jewelry, and dental or medical components. However, working with liquid resin can be messy and requires proper handling of chemicals and UV protection.
In summary, choosing the right 3D printing material largely depends on the specific needs and requirements of the project.
Understanding the unique properties and applications of PLA, ABS, filament, resin, and photopolymer resin will enable you to make informed decisions and achieve optimal prints.
Computer and Software Requirements
When diving into the world of 3D printing, it’s essential to know the computer and software requirements.
A budget computer with at least 8GB of RAM and a 2-core Intel or AMD processor should suffice for most 3D printing tasks. This setup will allow you to comfortably use any slicer, the software that converts 3D files into machine instructions.
A laptop or PC with a minimum of 4GB RAM will enable you to run 3D design software and slicing programs smoothly. Besides the hardware, a good internet connection is essential for downloading 3D models and updating your software.
In the 3D printing process, you will encounter STL files, which are standard formats for most 3D models. Hence, ensure your computer can access the internet to download these files and the necessary 3D printing software.
To create your own 3D models, you might choose to use professional CAD software, such as AutoDesk Fusion360 or Blender.
Keep in mind that 3D printing demands may vary depending on the specific printer and software used. Therefore, always verify the requirements of your chosen hardware and software.
By ensuring your computer and software requirements align with your 3D printing needs, you’ll be well on your way to a successful and enjoyable 3D printing experience.
Tools for 3D Printing
Every 3D printing professional requires a variety of tools to achieve perfect prints and maintain their equipment.
One such essential tool is the spatula used to safely remove finished prints from the build plate. This ensures minimal damage to both the print and the plate.
Pliers can be quite helpful too, particularly needle-nose and wire-cutting pliers. They come in handy when snipping away support material or trimming filament.
Blue masking tape is another widely used basic tool that helps to secure the build plate and improve print adhesion. To enhance adhesion further, consider using a glue stick or hair spray, which can be applied directly to the build plate.
Keeping filaments dry is essential for avoiding print defects. Utilize desiccants to absorb moisture and store your filaments in a dry environment.
Precision is key in 3D printing, and using a digital caliper allows you to measure parts accurately. Along with a caliper, a palette knife or an X-acto knife makes it easier to clean up any imperfect edges on your print.
A complete 3D printing toolkit should also include hex keys for maintaining and adjusting your printer, and tweezers to remove any excess filament or debris.
For post-processing, equip yourself with sandpaper in various grits to smooth out prints and achieve the desired finish. It’s also wise to have a set of screwdrivers to disassemble and reassemble your machine during maintenance.
A flashlight helps to illuminate hard-to-reach or poorly lit areas of your printer.
Lastly, a rotary tool, such as a Dremel, becomes invaluable when it comes to post-processing tasks like cutting, engraving, or sanding your prints.
With this collection of tools at your disposal, you’ll be well-equipped to handle any 3D printing challenge that comes your way.
The Printing Environment
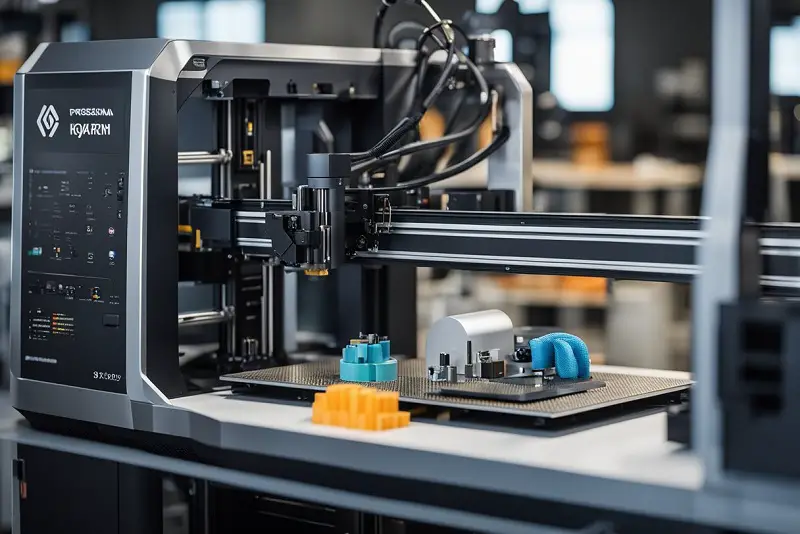
Creating an optimal printing environment is essential for successful 3D printing.
This includes proper ventilation, control of particles, setting up a functional workspace, and ensuring essential equipment is present.
Good ventilation is crucial to maintain air quality in the area where your 3D printer operates. 3D printers can produce fumes and unpleasant smells during the printing process, especially when working with certain materials.
Make sure the environment is well-ventilated to help dissipate these odors and maintain a comfortable workspace.
Managing particles generated during 3D printing is another important aspect of the printing environment. Some filaments release tiny particles into the air as they are heated, which can be harmful if inhaled regularly.
A workspace with proper airflow or an additional air filter can help reduce the concentration of these particles, promoting a healthier workspace.
Choosing a suitable location for your 3D printer is essential. Designate a dedicated workspace, such as an office or a designated printing room, to keep your printer and supplies organized.
This space should have a stable, flat surface to place your printer, as well as shelves or storage for materials and tools. Additionally, consider using an enclosure around your printer to maintain a consistent temperature and reduce noise levels.
Lastly, it’s essential to have an Uninterruptible Power Supply (UPS) in your printing environment. Power outages and fluctuations can cause print failures or even damage your printer.
A UPS can provide battery backup and voltage regulation, helping to keep your printer running smoothly and protecting it from potential damage.
By considering these factors and setting up a well-prepared printing environment, you’ll be able to optimize your 3D printing experience and achieve better print results.
Preparation and Post-Processing
When it comes to 3D printing, proper preparation and post-processing are essential for achieving high-quality results. In this section, we’ll discuss the equipment needed for these crucial steps.
Before starting the printing process, it’s important to ensure proper adhesion of the printed object to the build surface. One popular option is BuildTak, a thin and durable surface that helps prevent warping or curling.
Alternatively, you may also use other build surfaces tailored for your specific 3D printer.
To maintain a clean build surface and improve adhesion, consider wiping it down with isopropyl alcohol before every print. This ensures that any residue or grease is removed, providing the best possible foundation for your 3D print.
Equally important during the preparation stage is wearing nitrile gloves. These gloves protect your hands from harmful chemicals and help prevent potential contamination of the printing materials.
After a 3D print is complete, the post-processing stage begins with print removal. Carefully detaching the object from the build plate can be a challenging task, so utilizing print removal tools is highly recommended.
These tools come in various shapes and sizes, making sure your 3D-printed object is safely and easily removed.
Once the print is detached, it’s time for clean-up. Removing any leftover support material or imperfections requires tools such as pliers, flush cutters, and tweezers.
Precision is key at this stage, and using the right instruments will make all the difference.
Lastly, warping or curling can occur both during and after printing. If you have already used a high-quality build surface, this risk can be minimized.
However, if these issues persist, consider adjusting the print settings or experimenting with different materials to achieve the best results.
With proper preparation and post-processing equipment, your 3D printing experience will be enjoyable, and you will create high-quality, finished products.
Safety Considerations
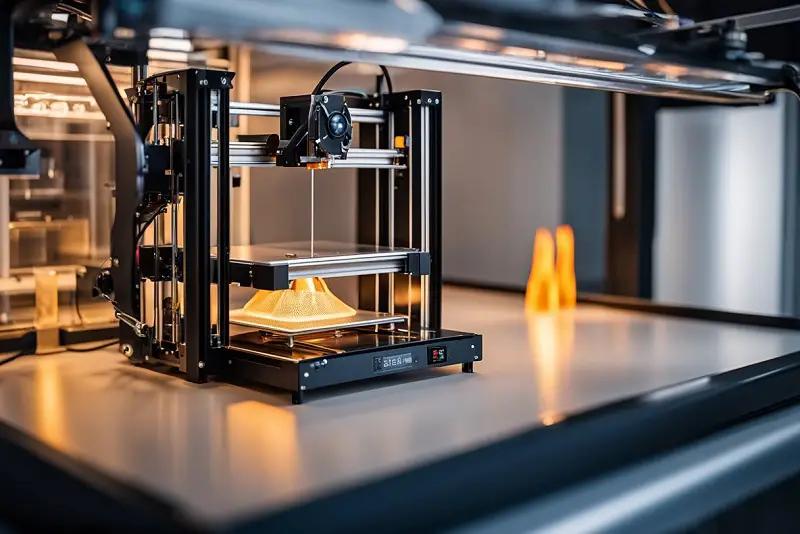
When working with 3D printers, it is essential to prioritize safety. One critical factor to consider is proper ventilation.
Utilizing a well-ventilated room with an open window or an exhaust fan can significantly reduce the concentration of harmful particles generated during the printing process, ultimately leading to a safer work environment.
The emission of ultrafine particles, fumes, and other nanoparticles during the 3D printing process may pose health risks, especially if inhaled.
To minimize this risk, it is crucial to maintain good ventilation and consider using filtration systems to capture and remove potentially hazardous particles.
Personal protective equipment (PPE) is another important consideration when working with 3D printers.
Wearing nitrile gloves can help prevent skin contact with chemical substances, while heat-resistant gloves are useful for handling hot printer components.
Goggles or safety glasses can protect the eyes from debris or splashes, ensuring that users are shielded from potential accidents or injuries.
Aside from these precautions, it is vital to always follow the manufacturer’s guidelines and recommendations for operating and maintaining 3D printers.
Proper training and familiarization with the equipment will enhance safety and mitigate the chances of accidents or prolonged exposure to harmful substances.
By taking these simple yet effective measures, individuals can enjoy the benefits of 3D printing technology while safeguarding their health and well-being.