3D printing has revolutionized the manufacturing world by enabling the creation of complex objects layer by layer.
Unlike traditional printers that use ink to transfer text or images onto a surface, 3D printers use a different approach to construct objects.
Rather than ink, these printers work with a variety of materials to create solid structures.
The materials used in 3D printing, commonly referred to as “inks,” vary depending on the type of printer and the desired end product.
Some popular materials include PLA, ABS, PETG, resin, nylon 12, powdered metals, and wax.
The main types of 3D printers that determine the “ink” used are Stereolithography (SLA) Printers, Selective Laser Sintering (SLS) Printers, and Fused Deposition Modeling (FDM) Printers.
Understanding the different types of materials and their unique properties is essential for anyone interested in 3D printing.
As the technology evolves, the range of materials compatible with 3D printers will undoubtedly expand, opening up endless possibilities for innovators and industries alike.
So, let’s dive into the exciting world of 3D printing materials!
Table of Contents
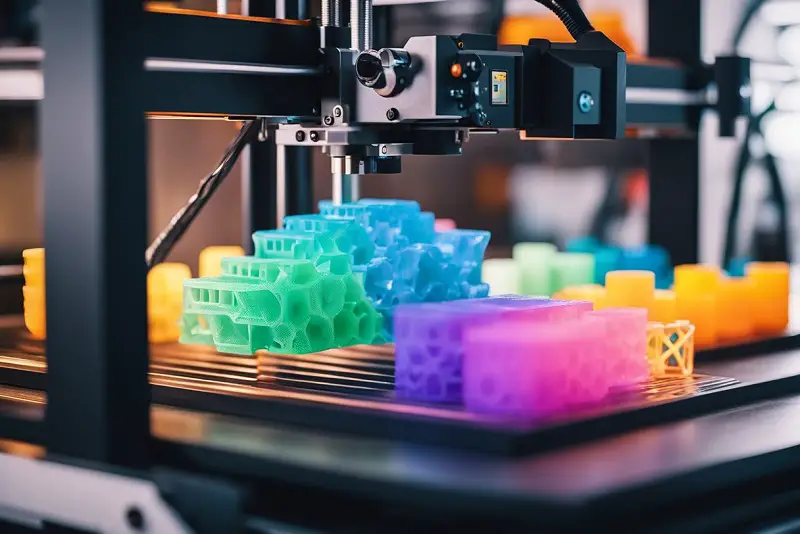
Types of Ink Used in 3D Printing
3D printing technology has evolved continuously, and various types of materials are used as “inks” in the process. These materials, often in the form of filaments or resins, enable the creation of diverse and functional 3D-printed objects.
ABS (Acrylonitrile Butadiene Styrene) and PLA (Polylactic Acid) are two common types of thermoplastics used in 3D printing. ABS is known for its durability and strength, making it suitable for manufacturing parts that require higher resistance.
PLA, on the other hand, is biodegradable and derived from renewable resources, such as cornstarch. It has a lower melting temperature than ABS and is easier to print with, making it popular among beginners.
PET (Polyethylene Terephthalate) and its modified version, PETG (Polyethylene Terephthalate Glycol), are other widely used thermoplastics in 3D printing.
PET is a strong and highly flexible material, commonly used in creating water bottles. PETG is more suitable for 3D printing applications, offering better layer adhesion and improved strength.
Resin, specifically liquid resin, is prevalent in Stereolithography (SLA) and Digital Light Processing (DLP) 3D printers. Resins are a type of polymer that hardens when exposed to specific wavelengths of light.
They offer higher resolution, and smoother surfaces, and are suitable for intricate details, making them ideal for creating prototypes and miniatures.
Conductive materials can also be used in 3D printing, particularly for printing electronic circuits and components. These materials combine metal nanoparticles or conductive polymers with standard printing materials, creating functional printed electronics.
Natural and composite materials are gaining popularity among environmentally conscious users. For example, wood, cork, or bamboo fibers can be mixed with PLA to create a more sustainable 3D printing filament.
Nylon 12 is a strong, versatile material with high resistance to wear and tear. It offers a balance of robustness and flexibility, making it suitable for functional parts in automotive, industrial applications, and more.
Metals, such as aluminum, steel, titanium, and gold, can be used in 3D printing processes like Direct Metal Laser Sintering (DMLS) and Selective Laser Melting (SLM).
These processes allow the creation of highly strong and complex metal parts ideal for various industries, including aerospace and medical.
Lastly, HIPS (High-impact polystyrene) is a popular material often used as support for ABS prints.
HIPS is a lightweight yet sturdy material that dissolves in a particular solvent (d-limonene) without affecting the primary print, making it extremely useful in creating complex structures.
Influence of Ink Viscosity
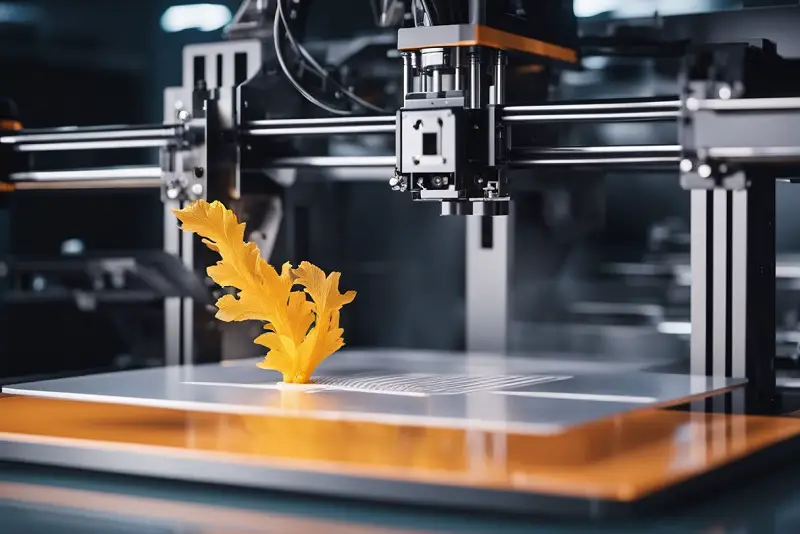
In 3D printing, the ink’s viscosity plays a crucial role in determining print quality and accuracy. Viscosity refers to a fluid’s resistance to flow, and it directly impacts the way the ink behaves during the printing process.
High-viscosity inks are thicker and generally adhere better to surfaces, while low-viscosity inks tend to be thinner and spread out more easily.
The rheological properties of the ink, which describe its flow behavior and the relationship between shear stress and deformation, are also essential for successful 3D printing.
Ideally, an ink should have a balance between viscosity and other rheological properties to exhibit acceptable adhesion, compatibility, and leveling. This balance ensures a smooth flow of ink through the print nozzle and onto the substrate.
In piezoelectric inkjet printing, for example, various factors affect the print outcome, including the ink’s viscosity and surface tension.
A study investigating the effect of viscosity and surface tension on inkjet-printed picoliter droplets found that for optimal printing performance, inks should satisfy specific rheological requirements.
When it comes to bio-ink in 3D bioprinting, a technology gaining traction in regenerative medicine and tissue engineering, the viscosity of the bio-ink becomes even more critical.
It should be suitable for the fabrication of highly complex structures and compatible with varying cell types.
In conclusion, understanding and controlling ink viscosity and rheological properties are vital factors for achieving high-quality, precise 3D-printed structures.
Manufacturers and researchers should carefully consider these properties when developing and selecting inks for their 3D printing applications.
Importance of Filaments and Printer Head
In the world of 3D printing, filaments play a crucial role as they are the primary material used to create objects.
These filaments are typically composed of thermoplastic materials, which can be heated, formed, and cooled without affecting their properties source.
Some of the most common types of filaments include PLA, ABS, PETG, and TPU, each with unique properties that make them appropriate for different applications.
Filament spools serve as the delivery system for these materials, feeding them through the printer and ensuring a consistent flow during the printing process.
Proper storage of filament spools is essential to prevent degradation, moisture absorption, and tangling of the filament.
The printer head, also known as the extruder, is another essential component of FDM printers. It is responsible for heating up the filament to a specific temperature and depositing it layer by layer onto the print bed in a precise pattern.
The performance of the printer head ultimately determines the print quality, layer resolution, and print speed of the final object.
One aspect that plays a crucial role in determining the printing quality and efficiency is the compatibility of the printer head with the chosen filament.
When printer heads and filaments are not well-matched, there can be issues in adhesion, material flow, and overall print quality.
In conclusion, choosing the right combination of filaments and printer head is essential for every 3D printing project. The compatibility between these components impacts print quality, efficiency, and the final result.
By understanding the unique properties of various filaments and the capabilities of printer heads, one can optimize the 3D printing process and produce high-quality, functional objects.
Role of Ink in Printing Resolution
In 3D printing, the type of ink used plays a significant role in determining the printing resolution.
Printing resolution refers to the level of detail that can be achieved in a printed object, which is crucial for ensuring accuracy and precision. A higher resolution generally results in a more detailed, smoother, and better-quality print.
In the 3D printing world, inks are commonly referred to as filaments or resins, depending on the type of printing technology utilized.
For example, Fused Deposition Modeling (FDM) printers use filament-like materials, while Stereolithography (SLA) and Digital Light Processing (DLP) printers use UV-curable resins.
Different inks offer varying levels of printing resolution, which ultimately impacts the print quality.
When aiming for higher printing resolutions, it’s essential to choose a suitable ink type that provides the necessary level of detail.
For instance, some materials can hold finer details more effectively than others, making them a better choice for high-resolution prints.
Additionally, some inks have better adhesion properties, which allows for smoother layering, particularly in the vertical (Z) dimension.
Furthermore, nozzle size and layer thickness are also crucial factors affecting printing resolution. Smaller nozzle sizes enable the printer to create finer details, while thinner layers result in higher-resolution prints.
However, it’s vital to consider the compatibility between the chosen ink and nozzle size – certain materials may not flow smoothly through smaller nozzles, which could lead to clogs or other printing issues.
In summary, the role of ink in printing resolution is undeniable. Choosing the right type of ink is crucial for achieving the desired level of detail in 3D-printed objects.
By carefully selecting the ink and ensuring proper nozzle and layer settings, one can optimize the printing resolution to produce prints with high precision and quality.
Inkjet Printing in 3D Printers
Inkjet printing in 3D printers is a versatile technique that allows for the creation of three-dimensional objects by depositing various materials layer by layer.
This low-temperature, low-pressure process works by utilizing a specialized printhead to precisely deposit liquid materials or solid suspensions onto a substrate.
Common materials used in inkjet 3D printing include polymers, dielectric nanoparticles, and conductive nanoparticles, making it adaptable to a wide range of applications.
The printhead plays a crucial role in the inkjet printing process. It consists of multiple nozzles that release the ink in a controlled manner, forming the desired 3D structure.
The accuracy and resolution of the final product depend on the quality of the printhead and its ability to efficiently dispense the chosen materials.
Inkjet 3D printing technology has seen numerous advancements in recent years, enabling the development of complex structures and devices. Some key benefits of this method include:
- High resolution: Inkjet 3D printers offer a high level of precision, making it possible to create intricate designs and structures.
- Material flexibility: The use of diverse materials enables the production of functional and multi-material 3D objects.
- Faster production: The process of inkjet printing has fewer steps compared to other 3D printing techniques, allowing rapid manufacturing.
These advantages have led to various applications of inkjet 3D printing, such as in the electronics industry, where it’s used for fabricating components like circuit boards and sensors.
Additionally, inkjet 3D printing can also be applied to other fields, such as biomedical and aerospace, as it enables the creation of custom-made parts with tailored properties.
In conclusion, inkjet printing has emerged as a highly adaptable and precise 3D printing technique, thanks to its ability to deposit a wide range of materials and operate with specialized printheads.
This technology holds immense potential for industries that require intricate designs, rapid production, and material flexibility.
Influence of Ink on Surface Finish
When it comes to 3D printing, the choice of ink plays a crucial role in determining the surface finish of printed objects. Different materials used in the inks can lead to various finishes, such as glossy or matte appearances.
One important factor in achieving a desired surface finish is the selection of a suitable 3D printing material.
For instance, certain materials such as those with embedded bacteria can lead to the creation of living materials that can be useful in various applications, from degrading toxins to facilitating organ transplants. The ink this 3D printer uses is alive. Watch it in action.
The surface roughness of a 3D-printed object can be greatly influenced by the quality of ink used.
It has been demonstrated that improving the surface finish of a 3D-printed part from around 4 micrometers to under 1.5 micrometers can drastically enhance the Pull-Out Force (POF) by a factor of 5. This highlights the importance of using high-quality inks when aiming for an excellent surface finish.
In addition to the choice of ink and material, various finishing methods can be employed to further improve the appearance and performance of printed parts. Some common finishing techniques include:
- Sanding: Manual or automated sanding can help reduce visible layer lines and improve overall surface smoothness.
- Polishing: Applying polishing compounds or using polishing machines can create a glossy or shiny surface finish on the printed piece.
- Painting: Protective or decorative coatings can be applied to enhance the appearance, mechanical properties, or chemical resistance of 3D-printed objects.
In conclusion, the choice of ink used in the 3D printing process has a significant impact on the surface finish of printed parts.
By selecting appropriate materials and applying suitable finishing techniques, a wide range of surface finishes, from glossy to matte, can be achieved for various applications.
Bioinks and 3D Bioprinting
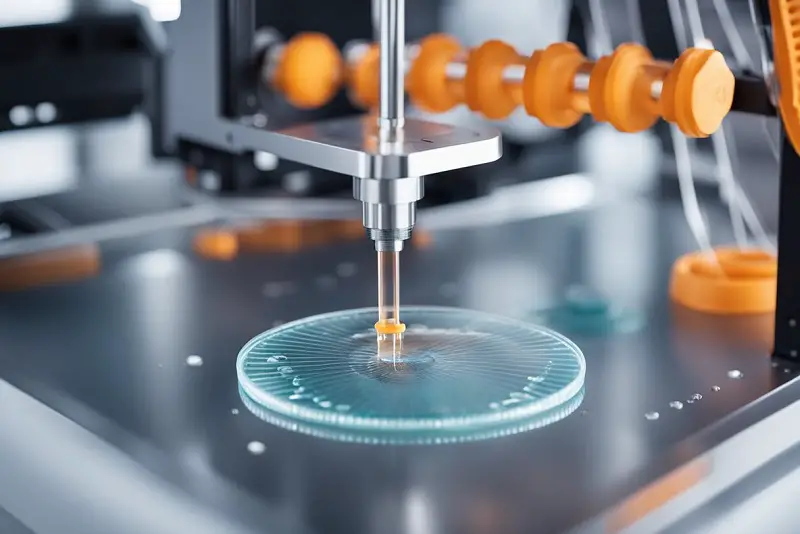
Bioinks play a crucial role in the process of 3D bioprinting, which aims to fabricate complex living tissue constructs for applications in regenerative medicine, drug testing, and even organ transplantation.
Bioinks are essentially a combination of living cells and biocompatible materials, typically in the form of hydrogels. These cell-laden bio-inks provide a supportive environment for the cells to thrive and develop into functional tissues.
3D bioprinting utilizes various techniques to create precise tissue structures, including extrusion-based bioprinting, inkjet-based bioprinting, and laser-assisted bioprinting.
Each method offers unique advantages in terms of speed, resolution, and complexity of the structures produced.
Regardless of the technique chosen, an ideal bioink must possess suitable mechanical, rheological, and biological properties to emulate the target tissue and facilitate proper functionality.
Hydrogels serve as the primary building blocks of many bioinks, as they offer several features that are essential for cell survival and growth.
Hydrogels closely resemble the natural extracellular matrix (ECM) found in our bodies, providing an environment in which cells can proliferate, differentiate, and communicate with each other.
Furthermore, their high water content enhances biocompatibility and allows for the transport of nutrients and waste products, thereby promoting healthy cell activity over time.
When creating complex, multi-layered, or vascular tissue constructs, scientists deploy multiple types of bioinks to achieve the desired results.
Vascularization is particularly challenging since it requires the integration of different cell types, structures, and biological cues that guide the formation of blood vessels.
Recent advancements in bioinks have enabled the generation of functional, perfusable vascular networks within 3D-printed tissues, bringing us one step closer to the successful printing of whole organs.
In summary, bioinks and 3D bioprinting work in tandem to provide an innovative method for creating advanced tissue constructs.
Through the careful selection and manipulation of bio-inks, researchers are honing their ability to generate complex, functional tissues with the potential to revolutionize medicine.
Limitations of Ink Materials in 3D Printing
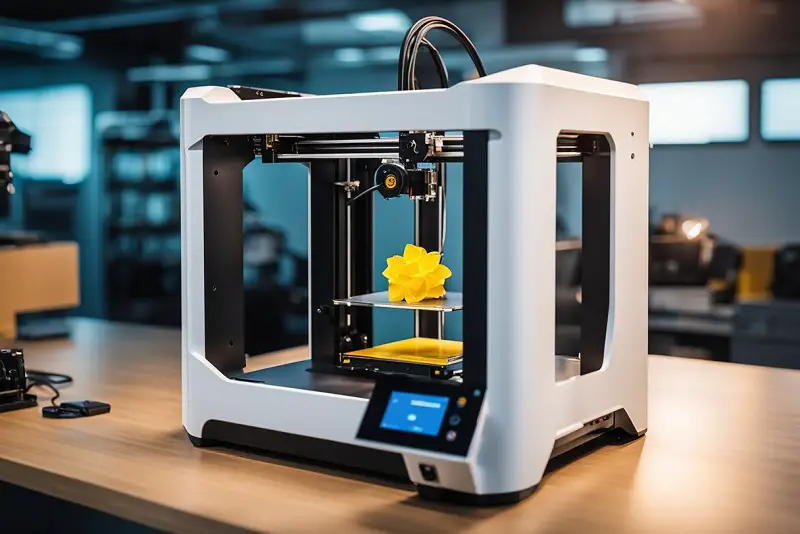
One limitation of ink materials in 3D printing is the trade-off between mechanical and physical properties.
Many materials used in the Digital Light Processing (DLP) process offer excellent precision and surface finish, but their mechanical properties might not be suitable for some applications.
This is especially challenging when producing functional prototypes or end-use parts that must withstand certain stress or strain loads.
Another constraint in 3D printing is the inability to produce parts on a large scale. While highly customizable parts can be produced efficiently with 3D printing, this technology struggles to compete with traditional manufacturing methods in terms of volume production.
This limits its application to industries requiring mass production or cost-effectiveness on a larger scale.
The choice of ink materials is also limited due to the need for compatibility with the printer’s print head or light-sensitive resins.
This restricts the available material options, making it difficult to find an optimal balance between mechanical performance, surface finish, and printing process.
In addition, 3D inkjet printing of electronics such as Printed Circuit Boards (PCBs) is a complex process, requiring a combination of conductive and insulating materials to be printed simultaneously.
This often poses challenges in achieving the high resolution and surface finish required for accurate and functional PCBs.
Lastly, the 3D inkjet printing materials should be adaptable to a broad range of materials to cater to various applications.
However, the available options of polymers, dielectric nanoparticles, and conductive nanoparticles may not satisfy the unique requirements of every project, limiting the effectiveness of the technology in some cases.